Daddy Cool
Liquefied gases, such as hydrogen, are generated, transported and stored at cryogenic temperatures near absolute zero. Such temperatures call for specially engineered valves capable of resisting these cryogenic temperatures. The Type 3248 Cryogenic Valve is such a valve; it is also suitable for installation directly in the cold-box. To facilitate installation and achieve an optimized flow of the liquefied gas, the valves are available with globe- and angle-style bodies.
No chance for embrittlement
All wetted valve parts are made of materials with defined alloy compositions. They withstand the extremely low temperatures, showing no signs of impaired strength and viscosity even after longer periods in operation.
Maintenance made easy
The valves come with a top-entry design. As a result, service and maintenance work on the trim parts can be performed without having to remove the valves from the pipeline, cold-box or insulation. After the actuator has been removed, there is free access to the valve seat and plug through the cryogenic extension bonnet.
Minimized emissions
Thanks to their bellows seal, the valves comply with the strictest emission requirements according to ISO 15848. Fugitive emissions are minimized and in hydrogen service the flammable, explosive gas is prevented from escaping.
Excellent reliability
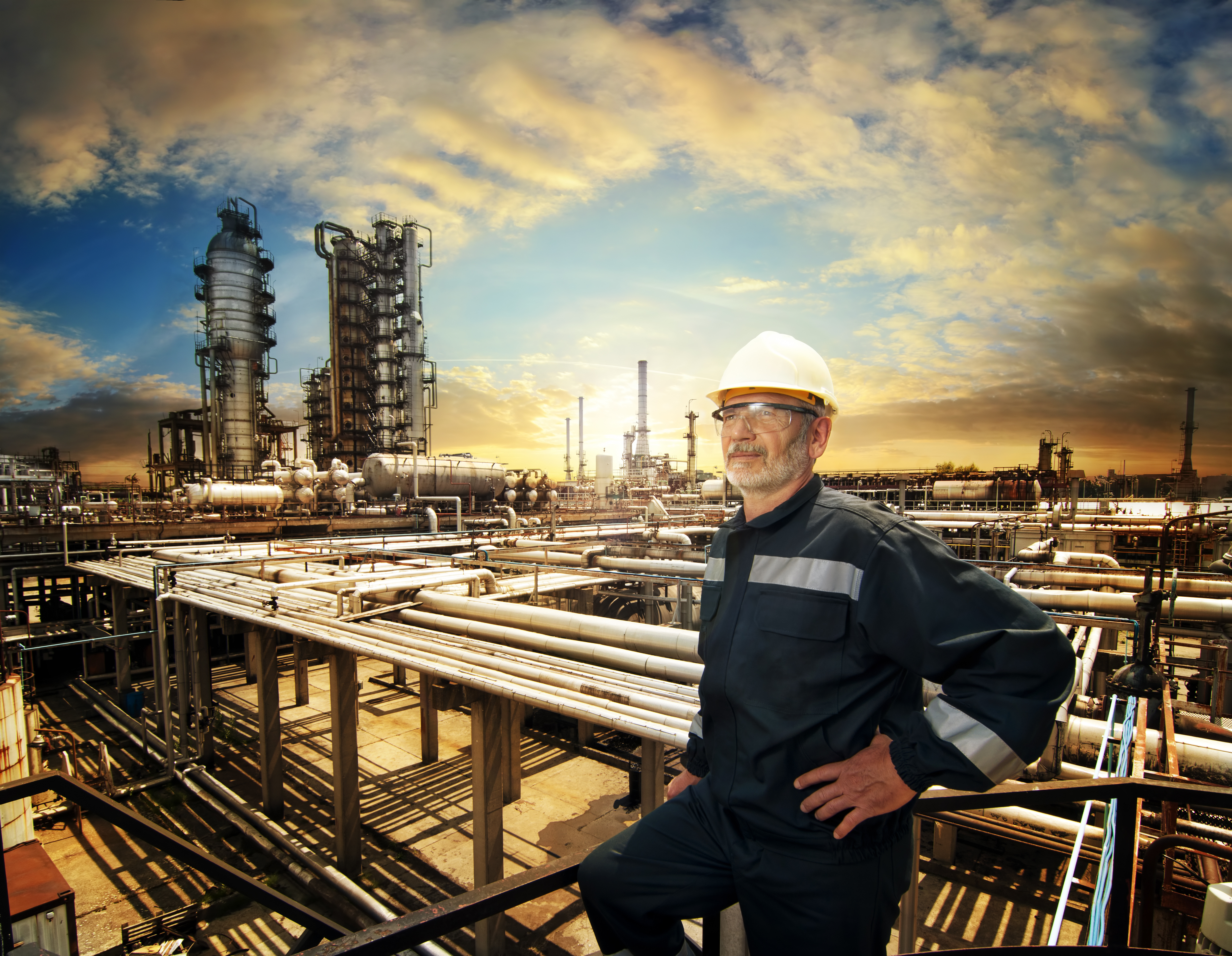
ACHEMA 2022
SAMSON valves for the hydrogen value chain
-
Hydrogen network feed-in
Hydrogen generated from renewable energy sources can be fed into existing (natural) gas networks. Once in the pipeline, it can be used in power generation or heat supply applications. This presents a sustainable solution for the storage and conversion in energy networks based on renewable energy sources.
-
Green hydrogen
The electricity required to produce green hydrogen is generated in solar-thermal power plants, for example. In such plants, solar radiation is bundled by reflectors (mirrors) to heat up oil, water or molten salt for the downstream generation of steam to generate electricity. SAMSON has the right solutions to meet the strict material and control accuracy requirements that apply throughout the entire process.
-
Electrolysis
Green hydrogen is generated by decomposing water into hydrogen and oxygen using renewable electricity. In the different procedures, precise, rugged control is necessary to guarantee the highest levels of efficiency and reliability in supply and the output stages across a wide load range. For years, products by SAMSON have been used successfully in our customers' plants.
-
Ammonia generation
Green hydrogen and nitrogen are fed into high-pressure reactors for the sustainable production of ammonia. Ammonia is more than an essential intermediate product in the production of fertilizers; it can also serve as a high-density fuel. To ensure proper control of the media at high temperatures and pressures, SAMSON valves are a proven, rugged choice.
-
Liquefaction and transport
Hydrogen is cooled down in several stages to liquefy it. The two main methods used are the Joule-Thomson effect and Claude's process. Tanker ships or tank trucks are used for transport. The SAMSON control equipment necessary for liquefaction and transport, which comes with a design temperature of –253 °C, has been proven in service for many years.
-
Refineries
In refineries, hydrogen is used in crude oil refining processes: In hydrocracking, hydrogen serves to break long-chain hydrocarbon molecules. In hydrotreating, hydrogen is used to remove sulfur and other unwanted compounds from petroleum products through hydrogenation. SAMSON has been supplying valves, actuators, explosion-protected positioners, limit switches and solenoid valves for these key applications for decades.
-
Hydrogen refueling stations
Hydrogen is stored as a liquid to reduce its volume. When refueling vehicles, the cryogenic hydrogen is evaporated and subsequently compressed before it is introduced into the vehicle tank. At many stations, SAMSON self-operated regulators are used to control the pressure during the evaporation process.
-
Chemical industry
The industrial-scale production of high-purity polysilicon for microelectronics and solar panels mainly takes place in a process that is based on chemical vapor deposition using trichlorosilane and hydrogen. Control valves by SAMSON even surpass the highest purity levels to be met and, thanks to exact control, they guarantee reliable operation, prime quality and high yields..
These industries work with our solutions










